Flatness Indication (FI) System
Flatness Indication (FI) System
Product Overview
The flatness indication (FI) system is an operation support system that detects the tension distribution during rolling using an integrated roller equipped with a highly sensitive quartz piezoelectric element and analyzes the detection signal to display the flatness of the rolled material.
In 1984, Kobe Steel entered into a technical partnership with the Institute for Applied Research (BFI) under the German Iron and Steel Institute (VDEh), and have designed and manufactured this system based on the basic patents owned by BFI.
Features of the FI System
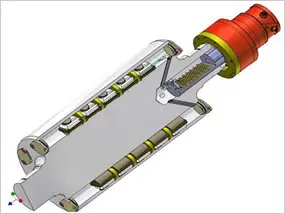
- Sensor-integrated detection roller
- Adjustable to any roller diameter and sensor pitch
- Surface treatment tailored to the process
- High accuracy, high-speed response
- High strength, wide temperature range
- Highly reliable communication via pulsed non-contact optical transmission
Features of the Software System
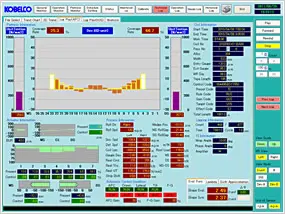
- A wide range of applications to meet user needs from sensing to the manufacturing execution system (MES) support
- Flexible system configuration tailored to the process
- Open system configuration: scalability, future potential, availability
Locations of Shape Detection Rollers
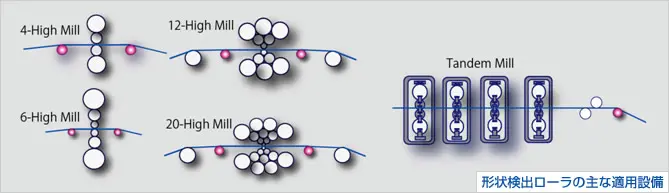
Automatic Flatness Control (AFC) System
Product Overview
Automatic Flatness Control (AFC) System imports the flatness data detected by Flatness Indication (FI) System and outputs the operating values to the rolling mill's flatness corrction actuators.
The system is based on a multi-variable control theory that was originally developed by our company utilizing our extensive experience with multi-high mills (KT and KST Mills) and aluminum foil mills (4-high).
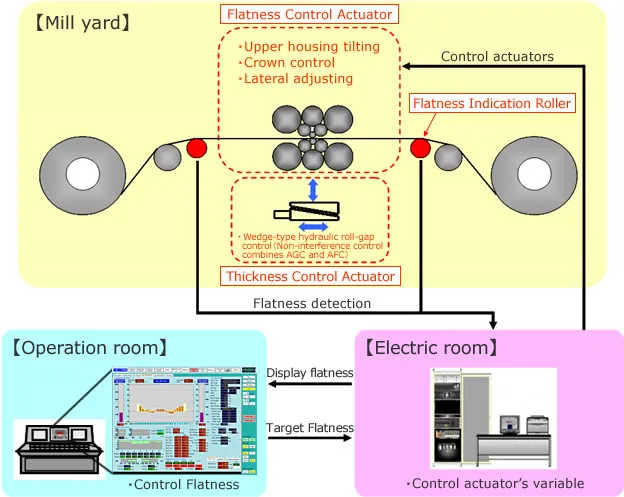
Flatness Control Algorithm
Based on the multi-variable control theory, this system determines the optimal operating values for flatness error correction by collecting and evaluating each actuator's flatness control capabilities (influence coefficients).
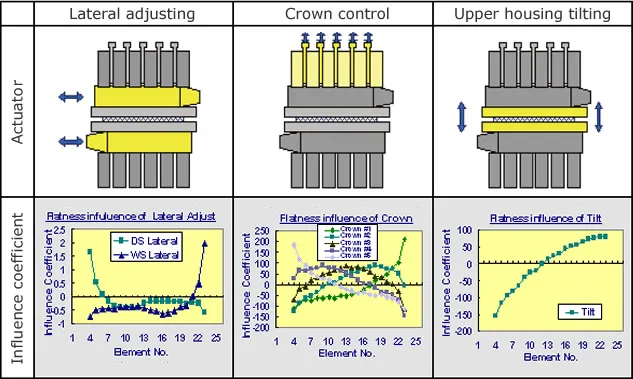
Non-Interference Control Model with AGC and AFC combined
Kobe Steel's patented non-interference control model minimizes the effect on plate thickness that occurs with the changes in operating values of the flatness control actuators.
It uses both an automatic gauge control (AGC) as upper non-interference control, which outputs the combination of actuators with the least effect on plate thickness, and an automatic flatness control (AFC) as lower non-interference control, which uses the wedge-type hydraulic roll-gap control system to compensate for minor plate thickness fluctuations.
Flatness Control Results
Optimal flatness control for various types of rolling mills is achieved by collecting and evaluating each actuator's influence coefficients.
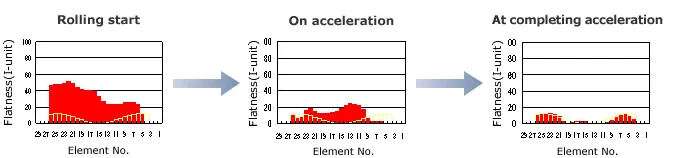
Kobelco Operation Support System (KOS)
Product Overview
Kobelco Operation Support System (KOS) is an integrated monitoring and operation system that displays various monitoring data, including the process conditions and schedule status of the rolling mill.
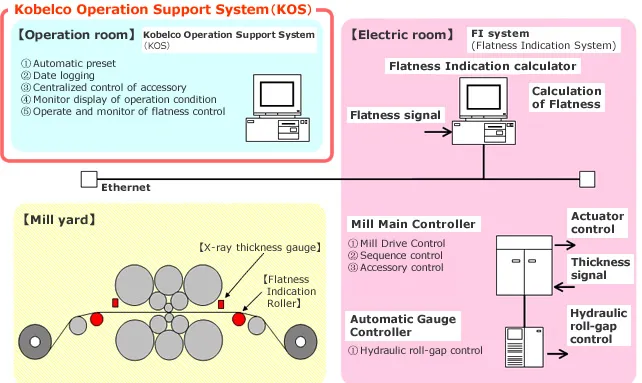
Main monitor of Kobelco Operation Support System (KOS)
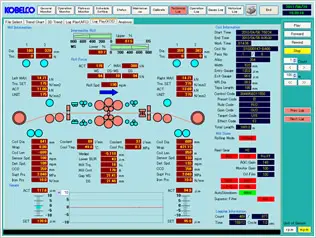
- Coil schedule monitor
- Pass schedule monitor
- Coil start/end time logging monitor
- Rolling process logging monitor
- Maintenance monitor
Technical Materials
Contact Us
You can reach us by clicking the inquiry button.